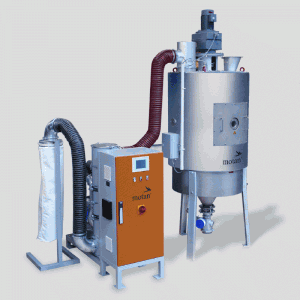
PET is indispensable not only in the market for water and soft drink beverage bottles, but also in thermoformed packaging and even as high-tech fibres for clothing. Worldwide polyethylene terephthalate consumption has grown considerably and it continues to grow at a rapid rate. This growth has resulted in worldwide consumption reaching more than 20 million tonnes in 2010. North, Central and South America continue to show significant growth rates, as do Asia and Europe. PET exhibits excellent properties – crystal clear transparency and a high gloss surface that are highly valued by packaging designers. Low weight, combined with high strength and shatter resistance, along with the ecological value of numerous recycling possibilities provides this material with a bright future. Those interested can learn more about this subject at the motan-colortronic stand B1-1111 in Hall B1, during the FAKUMA Exhibition in Friedrichshafen, Germany, 16th to 20th October 2012.
The crystallisation of amorphous PET is a key element in its preparation before it is processed in preform injection moulding machines and downstream stretch blow moulding machinery, or in sheet or film extrusion lines. Critical points in the crystallisation process are production start-up, agitation of material during its transition phase and dealing with dust. HDC series crystallisers from motan, together with motan LUXORBIN C agitator bins, master all these requirements – and in addition offer the processor flexibility through its modular design, easy operation and significant energy savings.
Modularity of the motan HDC crystallisers is represented by the wide range of nine heating modules and their highly efficient heating, blowing and control system functions, which provide throughput performance between 120 and 3,000 m³/h of process air. The customer benefits furthermore with the LUXORBIN C agitator bins from a choice of eight size combinations with bin volumes between 125 and 2,500 litres. This wide range of differently sized modules have enabled motan to design its crystalliser product program for hourly throughput quantities ranging from just 80 kg/h all the way up to 900 kg/h. Crystallisation quality is protected in the event of variations of material throughput within each module by automatic control of the material take-off rate. Process security is a top priority and is ensured in motan-colortronic’s equipment by the use of high strength torsion-resistant agitator arms and stators which can withstand the large forces to which they are exposed during the crystallisation process. As a further measure, the agitator motor will automatically switch off in order to prevent damage, should unexpected yet unacceptably high forces arise in the agitator bin.
Energy saving features: the frequency-controlled blowers continually adjust the amount of process air according to the input material temperature. The customer has a wide choice of options, as he can also equip his motan crystalliser with a rotary valve to discharge the material, cyclone dust separators and extraction equipment for material re-circulation. But in the standard version the line is already ideally equipped, with an air extraction filter and pneumatically operated slide discharge valve at the bin outlet.
The user-friendly control and monitoring system provides the operator with the best tool to manage the equipment. The touch panel, supported by a Siemens S7 programmable logic controller (PLC) working in the background, guides the operator with its clear self-explanatory graphic display. Most process parameter values are pre-installed. The operator only needs to enter an easily manageable amount of data relating to the product. Open process management makes a significant contribution towards preventing hydrolytic degradation of the material and low relative humidity of the process air – a particular feature of motan-colortronic crystallisers – results in good material drying. An additional advantage with motan crystallisers is that an automatic start-up program for the crystallisation of amorphous PET means that start-up of the crystallisation production process if required can be programmed and controlled by the production manager from his office.
Crystallisers are most efficient when running for long periods. Should cleaning or maintenance be required at some time, e.g. due to changes in material or production lots, these can be easily accomplished. The bin cone has been designed so that the lower section can be removed, enabling full and unrestricted access to the lower bin area. The large cross-sectional areas of the lower agitator bearings are ideal for good material flow and subsequent cleaning.
The motan Group
The motan Group, with its headquarters in Konstanz on Lake Constance in Germany, was founded in 1947. As the leading provider of sustainable materials handling, the company is active in injection moulding, blow moulding, extrusion and compounding, in-line and chemicals. Part of the application-orientated product spectrum are innovative modular systems solutions for the storage, drying and crystallisation, for the conveying, dosing and mixing for plastics manufacturing and processing industries. Manufacture takes place at various production locations in Germany, India and China. motan distributes its products and systems solutions via its regional motan-colortronic centers. Currently, more than 450 employees contribute to an annual turnover of approximately 100 million Euros. As a result of its network and its many years of experience, motan offers its customers what they actually require: solutions with genuine added value.