The Free State of Saxony is investing in the lightweight construction technology of the future as part of the German Federal Government’s Cluster of Excellence MERGE “Technology Fusion for Multifunctional Lightweight Structures” with the Chemnitz University of Technology.
A KraussMaffei MXW 2500 injection molding machine is installed at the new MERGE Lightweight Technology Center for researching and prototype manufacturing close-to-production in their original size.
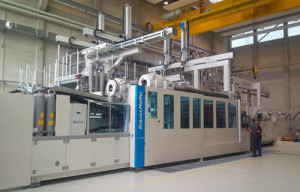
The ceremonial launch of the new plant took place in October 2015 as part of the 2nd International MERGE Technologies Conference.
“The KraussMaffei MXW 2500 injection molding machine is a true all-round talent in the area of lightweight construction with its numerous options in material, mold or process selection and it is certainly unique in the German research landscape in this design and size,” explained Georg Holzinger, Vice President of Technologies at KraussMaffei.
He emphasized that it is particularly important for the automotive industry to test the properties of lightweight parts at a 1:1 scale.
“We were deliberate in choosing a large machine with a clamping force range of 25,000kN to be able to represent large components with measurements of up to 1.5×1.5m at a close-to-production 1:1 scale,” added Prof. Dr.-Ing. Lothar Kroll, Director of the Institute of Lightweight Structures (IST) at the Chemnitz University of Technology and Coordinator of the MERGE Cluster of Excellence.
The MXW 2500 has a modular design that offers a wide range of configurations. The “W” code stands for “Wendeplattentechnik” (swivel plate technology), which helps to increase cost-effectiveness in multi-component injection molding based on KraussMaffei’s SpinForm technology.
With the TwinForm variant, KraussMaffei created an additional solution with a special multi-daylight mold that also ensures noticeably higher production. An additional bolt-on unit in an L-design enables the flexible, additional metering and processing of thermoplastics as well as thermoset matrix materials.
An additional mixing and metering system also enables the processing of polyurethanes (PU) with fillers and other reactive matrix materials. The 40-15/29 hybrid is equipped with a color-metering unit directly on the mixing head and an additional gas charging unit. This offers maximum flexibility during prototype manufacturing.
The new MERGE research system is also designed for what is called the MuCell process developed by Trexel, a KraussMaffei partner.
“The MuCell process has become an established technology, particularly in vehicle manufacturing and for technical components. The trend is moving towards also using this procedure for premium quality surfaces in visible components,” explained Holzinger.
Prototyping of thermoplastic lightweight construction with fiber-reinforced plastic is possible based on the FiberForm process developed by KraussMaffei. In this process, impregnated fabric or roving made out of continuous fiber, what are called fiber components, are heated, shaped in the injection mold and subsequently back-injected with a thermoplastic matrix.
In addition, two LRX500-TwinZ robots have replaced four LRX robots in the system supplied to the technology center. This type of robot (TwinZ) couples two x/y kinematic units each to the z-axis mechanically. Both robots can be programmed and operated using the multiple kinematics control concept. Integration of up to 24 axes is possible.
Website: www.adsalecprj.com