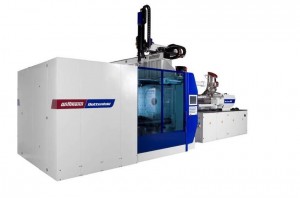
At this year’s Fakuma, held from 16 to 20 October in Friedrichshafen/Germany, WITTMANN BATTENFELD is presenting latest injection molding technology combined with high-tech processes in hall B1, booth 1204. The main focus at this year’s event will be on CELLMOULD®, the light-weight construction technology developed by WITTMANN BATTENFELD.
Reliability paired with continuous innovation – this is how WITTMANN BATTENFELD achieves sustainable customer benefit. Last year, the company succeeded in further developing its proven PowerSeries and now offers its large machine model MacroPower with clamping forces ranging from 400 to 1,100 t. But WITTMANN BATTENFELD also shows its power by developing and implementing innovative processes which open up new opportunities for excellence and high quality standards in plastic parts and materials to be processed. CELLMOULD® light-weight construction technology and optimal surface quality through BFMOLD™ will be demonstrated on 2 exhibits.
CELLMOULD® application NEW: MacroPower XL 550/5100 with CELLMOULD® light-weight technology
In the area of injection molding machinery, the MacroPower XL 550 will be presented for the first time at the Fakuma 2012. This is the 550 t machine model featuring extra-wide platens with a distance of1120 mm x 970 mm between tie-bars. The MacroPower stands out by its minimal footprint, high speed, modularity, absolute precision and cleanness. Its modular concept makes this new large machine suitable for a great variety of applications. The linear guides supporting the moving platen ensure a clean mold space as well as maximal, high-precision mold protection. The MacroPower reaches its velocity with high movement speeds and extremely short locking and pressure build-up times, which are achieved with the QuickLock locking system developed by WITTMANN BATTENFELD.
Another feature of the MacroPower calling for special attention is its facility for easy mold insertion from the rear of the machine.
At the Fakuma, the functionality of the MacroPower will be demonstrated by the production of an ABS housing with a tandem mold supplied by Coko, Germany, using the CELLMOULD® light-weight construction process. CELLMOULD® is a process for manufacturing structured foam parts, in which nitrogen is added directly in the barrel during plastification. The entire manufacturing equipment, such as the plastification unit, injectors, gas flow regulator and nitrogen generator, has been developed and built by WITTMANN BATTENFELD. This process enables the production of extremely light and rigid components without sink marks. A W843 WITTMANN robot will take care of removing the parts and depositing them on a conveyor belt. The functions of the entire production line are fully integrated in the machine’s B6 control system.
Highlight: CELLMOULD® plus BFMOLD™ technology – light weight combined with high-gloss surface
On a hydraulic HM 110/525 machine model, a combination of the BFMOLDTM and CELLMOULD® processes will be demonstrated by producing a desk telephone cover within a cycle time of 34 seconds in a single-cavity mold supplied by KIMW. In the BFMOLD™ process, the entire mold space underneath the cavity is utilized for heating and cooling. This enables extremely even and, above all, fast heating and cooling of the mold areas. With the help of BFMOLD™ technology, in particular, it is possible to produce parts with premium surface quality without any visible flow lines or sink marks. In this way, a perfect “piano black surface” can be achieved for foamed parts manufactured by the CELLMOULD® process. Moreover, this machine has been designed as an insider solution, which means that the WITTMANN robot for parts removal, the conveyor belt as well as the peripheral equipment for upstream and downstream processing are all integrated in the machine frame. The finished parts are removed and deposited on a conveyor belt by a W818 robot from WITTMANN.
Multi-component technology: thermoplastic resin plus LSR
On an HM 180/350H/350V ServoPower, the LIM process will be demonstrated in a 2 C application by manufacturing a spectacle case in a mold supplied by Rico. This spectacle case is a 2-component case made of a combination of thermoplastic material (PBT 20% GF) and LSR. The dosing and mixing pumps for the LSR will be supplied by 2 KM. TEMPRO plus D temperature controllers will be used to generate the high mold temperature required for vulcanizing the LSR. The machine comes with a silicone processing equipment package (special injection unit, vacuum package, etc.). The servo-driven rotary unit is integrated in the machine. The parts are manufactured in a 1+ 1-cavity mold within a cycle time of about 50 seconds.
The machine’s ServoPower drive technology also enables extremely energy-efficient operation.
High-precision micro injection molding
WITTMANN BATTENFELD’s expertise in micro injection molding will be demonstrated with an interesting application from the field of optoelectronics. A MicroPower 15/10 will be shown manufacturing a POM barrel holder with a mold supplied by Wittner/Austria. This part is a focusing instrument for lenses used in cameras, to focus the lenses and hold them in place.
The special feature of this part is a thread with an unscrewing core, which means that, following the injection molding process, a threaded core is screwed back directly in the mold, before a WITTMANN W8VS2 robot specially designed for this machine removes the part, then presents it for inspection to a camera integrated in the machine’s control system and finally deposits it on a conveyor belt, sorted according to cavities.
EcoPower with IML process
For the first time at a trade fair, an EcoPower with an IML application will be on display. The EcoPower is the extremely energy-efficient, all-electric machine from WITTMANN BATTENFELD’s PowerSeries. The EcoPower’s high energy efficiency is achieved by completely utilizing the deceleration energy from its drives within the machine (which would normally be returned to the power supply network by an elaborate process) to provide the necessary voltage for the control system, and for barrel heating. At the Fakuma, bank cards will be produced from a bioplastic material (PLA) on an EcoPower 180/750 with a 4-cavity mold, using the IML process. A WITTMANN W837 high-speed robot operating from the side will insert printed labels and blank labels prepared for individual printing into the cavities and remove the finished parts from the mold. The cards will subsequently be presented to a camera for inspection, to check the position of the labels.
WebService round the clock
The exhibition program of WITTMANN BATTENFELD is rounded off by a presentation of its WebService 24/7. WebService 24/7 stands for the online service from WITTMANN BATTENFELD, which is available round the clock on 7 days a week. Visitors to the Fakuma will have an opportunity to experience the operation of WebService 24/7 first-hand via a live connection at the service center specially installed for this purpose. This service center provides information to visitors about the other services offered by WITTMANN BATTENFELD as well, such as customer support, application technology, training, or the Battenfeld K4 production data acquisition system.