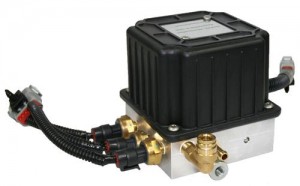
Design and systems engineers are often challenged with integrating many functions into a fluid control system application, while also having to minimize the size, cost, and complexity of the overall system design. This is often difficult to achieve, as today’s sophisticated fluidic systems must combine many individual components, often resulting in an overly complex design.
Manufacturers of fluid control devices are now offering their customers a system approach — an integrated system design that combines a number of components into a subsystem, typically utilizing a custom-designed manifold.
All in a day’s work
A typical fluid control system can contain a multitude of individual functional components, ranging from pumps and filtration components to various types of valves, regulators, and sensors. These components are typically interconnected via fluid conductors such as threaded pipe, rigid or flexible tubing, and fittings in what often becomes an oversized and over-designed system that is difficult to install and service. These connections create potential leak paths, which are especially undesirable in systems using oil, chemicals, or corrosive materials.
They can also introduce internal contaminants to the system, including thread slivers and bits of thread sealant, such as Teflon tape and pipe dope. In addition to the design task, the design engineer must also specify and often purchase all the individual components for system prototyping and production, which can be expensive and labor-intensive to assemble, particularly in high-volume applications.
Manifold alternative: keep it simple
Manifolds are routinely used in many industries, including both fluid control and fluid power applications. Many manufacturers of fluid control components offer products that are specifically designed for manifold mounting.
One of the most common reasons for design engineers to consider a manifold design is to minimize system size. The size of most fluid control components (for example, a valve) is often dictated by the body containing the internal working components, as well as the process connections, often threaded female ports for piping into the fluid control system. Since the body must contain both internal fluid pressure and provision for connecting to external piping, it is generally over-designed and over-sized for most applications.
A fluid control system employing many individual control components is a multiplication of this idea. A properly designed manifold becomes the “body” for as many system components as it makes sense to design into it. In general, engineers should consider an integrated system design for their fluid control applications in the following cases:
- High complexity/multiple functionality of a system, requiring numerous control components
- Space or size constraints within an overall application
- Significant production volume (typically thousands per year)
- High reliability
- High serviceability.
A closer look at the benefits
The benefits of using an integrated system design concept are many. Reduction in component connections minimizes the risk of leaks, which, in turn, minimizes the need for servicing and reduces customer returns and warranty costs. Subsystem assemblies make assembly of a larger system much easier, whether in the field, or on the production floor. With fewer connections to make, it takes less time to install, and often results in a more secure installation.
A custom manifold assembly can be designed to make servicing easier for the overall fluid control system. Easy access for strainers or filters can be designed in to ensure that recommended system maintenance procedures are easily followed. Critical component locations can be pre-designated for ease of adjustment or servicing. Maintenance or repair on one part of the system will also be less likely to disturb other parts of the system.
It is no longer unusual for the system design engineers to also be responsible for managing the supply chain for their designs — having to buy, stock, and manage the inventory necessary to prototype the system themselves. It’s especially helpful in these cases to be able to work with the supplier’s engineers to design an integrated system solution that will perform to the required system specification. This approach allows the design engineer to focus on the overall system design and results in significant time and cost savings.
Source: http://www.designnews.com/author.asp?section_id=1365&itc=dn_analysis_element&doc_id=261148&page_number=1