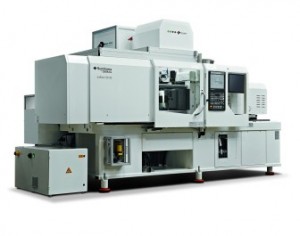
Macam Srl, the Italian agency of the injection molding machine manufacturer Sumitomo (SHI) Demag Plastics Machinery GmbH, will host a Technology Day event from April 17-19 at its facilities in Rivoli, Italy. Sumitomo (SHI) Demag, Ghilardi Stampi, Yushin Precision Equipments and Macam will be providing tips in all aspects of plastic processing. The lecture program will be rounded off with a paper presented by Turin Technical University (Polimeri al Politecnico).
The lectures will be repeated on all three days, taking place during the morning of each day. Following a shared business lunch, it will be possible to see machines, automation systems and other accessories in action during the afternoons. In addition, an evening event is planned on April 18. At the technology day, the smallest model in the IntElect range, an IntElect 50-45 with 500kN clamping force, will be manufacturing rotary knobs with a diameter of 3.5mm made from polyoxymethylene (POM) for hearing aids, in a cycle time of 10s. The moldings weighing only 10mg, and the shot weight of only 280mg. As said, the IntElect, with its precise and sensitive drives as well as the removal system integrated into the machine, meets the special requirements for zero-error production.
The four-cavity hot channel mold with submarine gate was designed and built by Stamm AG of Switzerland. The cabin suitable for clean room operation and the laminar flow unit above the production system are supplied by Max Petek Reinraumtechnik in Germany. The Filter Fan Unit (FFU) of the laminar flow unit cleans the drawn-in outside air, ensuring a constant laminar airflow over the mold installation space of the machine. It ensures a clean room category of ISO 7 in a corresponding production environment, preventing the ingress of particles. Germany-based MAi GmbH & Co. KG integrated the six-axis robot from Yaskawa Europe GmbH into the injection molding machine, the housing of which was only extended by 700mm on the non-operating side.
The robot is mounted suspended from the fixed mold clamping plate. According to SHI, this concept offers the benefits of keeping the clean room compact, reducing the masses to be moved and shortening the stroke distances of the robot. Also, it cuts the risk of sensitive moldings becoming contaminated on their way from the molded part removal through the inspection station and onward to packaging. The rotary knob is moved for a fully automatic 100% visual inspection while still within the clean room cabin. Other exhibits include a hybrid El-Exis SP 200-920 and a hydraulic Systec 210-1450.
Source: http://adsalecprj.com/Publicity/MarketNews/lang-eng/article-67004103/Article.aspx