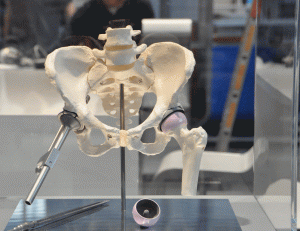
Since the first hip replacement was performed in 1960, the operation has mushroomed. More than 285,000 total hip replacements are performed annually in the United States, according to the U.S. Agency for Healthcare Research and Quality.
The technology has evolved significantly, and not always successfully. Materials’ issues have been blamed in some failures.
Some physicians are calling for a prohibition on artificial joints made of cobalt-chromium alloys in which the joint’s metal ball rubs against its metal socket. Poorly designed or positioned metal-on-metal implants can lead to release of elevated cobalt-chromium ion levels into the blood. The result can be damaged organs and inflammation. Metal ions are also suspected carcinogens.
Researchers at the Fraunhofer Institute for Manufacturing Engineering and Automation IPA in Stuttgart, Germany, feel they have found a solution with an implant made from polyetheretherketone (PEEK), a plastic whose specification has been exploding for internal body use despite its high cost. PEEK’s benefits include high strength and biocompatibility.
Carbon composite
The Fraunhofer hip socket is made of carbon fiber-reinforced PEEK. For the femoral head, ceramic is used. A hydroxylapatite coating at the interface to the bone helps ensure that the bone tissue will fuse thoroughly with the surface structure of the implant.
“The cobalt-chromium implants in use to date are very rigid, and the load transfer to the bone is non-optimal, leading to potential adverse bone adaptation,” says IPA engineer Jasmin Hipp. “Thanks to the new combination of materials, the transmission of force through the PEEK hip socket to the pelvic bone is modeled on natural conditions. And there are no metal ions released.”
Hipp’s team said they confirmed the good wear resistance in initial tests of the new hip replacement using a robot that simulated various series of movements such as walking or climbing. The experiments used a prototype of the implant.
European Commission project
The PEEK implant has been developed through a project called “ENDURE” (Enhanced Durability Resurfacing Endoprosthesis) that has been funded by the European Commission.
The ENDURE implants follow the bone-preserving principle of hip resurfacing: they are thin-walled shells that replace the bearing surface of the joint articulation alone, instead of employing large metal stems for support. Metal stems require a substantial volume of bone to be removed.
According to a Fraunhofer press release, researchers have also redesigned the way the prosthesis is mechanically attached to the bone. A press-fit is used instead of cement. The hemispherical ball and socket are tapped onto a prepared femoral head and into the acetabulum—the natural, concave surface of the pelvis—and anchored in place. An integral scaffold-type structure on the surfaces of the implant is in contact with the bone.
The researchers at IPA have developed a scalable tool that attaches the implant to standard surgical instruments, enabling implantation, re-alignment and removal. The tool can be discarded after a single use.
The challenge is to attach instruments to the very thin-walled cup implant with sufficient strength for implant repositioning. The instrument uses a collet pin combination.
The scientists are seeking patent protection for the invention, which has been tested on cadavers.
Final development work is under way prior to formal clinical studies. Partners in the project are Aurora Medical, Medicoat, Hunt Developments, Ala Ortho, CeramTec, Invibio, Biomatech and the Universities of Gothenburg and Southampton.
Manufacturing issues remain
It’s not clear how the PEEK implant would be manufactured. Two candidates would be injection molding and additive manufacturing. Surgeons at Walter Reed Army Medical Center in Washington D.C. have pioneered work on cranial implants, but chose not to use PEEK because of its high cost. Titanium is being used in custom implants produced through additive manufacturing.
According to sources who asked not to be identified, medical PEEK costs close to $400 per pound compared to about $44 per pound for industrial-grade PEEK.
The expense and suffering caused by hip replacement failures may warrant the additional cost. According to the ENDURE project, there are approximately 800,000 hip operations annually in Europe costing an average of €1942 ($2556) per implant. Some €2.3 billion ($3 billion) is spent annually on revisions. One of the issues is the increasing number of surgeries done on younger people. ENDURE says that 10% of all the prostheses implanted are in patients under 55 years of age—of which 33% fail within 16 years.
Source : plasticstoday.com