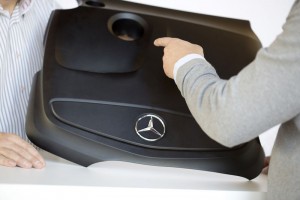
Mercedes-Benz has chosen a high performance polyamide largely made from renewable resources for the engine beauty cover of the brand-new Mercedes-Benz A-Class. Around 70% of the raw materials used to make the polyamide 410 in DSM’s EcoPaXX® Q-HGM24 reinforced compound are derived from the castor plant (Ricinus communis).
The engine cover, used on turbo-powered petrol-engine versions of the new A-Class, has to meet very demanding performance specifications, which are complicated by its large size. With dimensions of 575 by 550mm, and operating in an environment that can reach temperatures more than 200°C, resistance to warpage and high dimensional stability are important.
In addition, the engine cover is required to resist high dynamic loads deriving from engine vibrations, and it needs to be light. Mercedes-Benz’s target was to develop the new A-Class with better fuel-efficiency than the previous generation, and in fact, overall consumption has been improved by 26 percent. On top of this, the beauty cover is the most visible component in the engine compartment, so when the customer opens the hood, surface finish is paramount.
EcoPaXX Q-HGM24 has very good heat resistance, demonstrated by a deflection temperature under 1.8 MPa load (DTUL) of 200°C. The beauty cover, which weighs just 1.320kg, can survive continuous-use temperatures of 200°C, with short term peeks of 235°C. The compound, which contains glass fiber and mineral particulate reinforcement, produces a better surface appearance than any other polyamide currently used for this type of application.
This is the first time that EcoPaXX Q-HGM24 has been used for high volume mass-production, and according to Kees Tintel, EcoPaXX business manager at DSM, more will follow. “DSM launched EcoPaXX in 2009 in answer to increasing market demand for high performance durable bio-based engineering plastics,” says Tintel.
Mercedes-Benz states in the Life Cycle Environmental Certificate for the A-Class that production of an engine cover in bio-based polyamide results in only around 40% of the quantity of carbon dioxide emissions that would be necessary in order to produce the same component from a conventional polyamide. “The difference per component is around 6.5kg of carbon dioxide emissions,” says the report. “This technology makes a significant contribution towards climate protection.”
“EcoPaXX is 70% bio-based, but its “green” credentials come at no cost to performance,” says DSM’s Tintel. “It combines superb mechanical properties with excellent chemical resistance in various media. It also has the highest melting point of any bio-based aliphatic polyamide, making it very suitable for applications needing high heat resistance, such as engine covers for turbo engines and crank shaft covers. The fact that it can be used in so-called beauty covers in cars made by a company like Mercedes-Benz, which puts so much emphasis on the perfect marriage of form and function, speaks volumes for the surface finish it makes possible.”
BBP Kunststoffwerk Marbach Baier GmbH is the supplier for the engine cover. BBP build the production tooling including optimization and process fine tuning which is needed to reach the requested dimensional and surface requirements of Mercedes-Benz.
Since the launch of EcoPaXX, DSM has developed a full portfolio of polyamide 410 grades tuned to the needs of the automotive and other specialty industries. “It is really exciting to develop applications with a high-performance green material such as EcoPaXX, in such close cooperation with a major customer like Mercedes-Benz,” says Tintel “This is just the beginning and the real up-swing in use of bio-based products is soon to come.”
Mercedes-Benz concludes in its Life Cycle Environmental Certificate:
“The Mercedes-Benz A-Class not only meets the highest standards in terms of safety, comfort, agility and design, but also satisfies all current requirements with regard to environmental compatibility. This environmental certificate documents the major progress which has been achieved in comparison to the preceding model of the A-Class.
Moreover, a higher proportion of high quality secondary raw materials and components made from renewable raw materials is used. In all, the 2012 model year A-Class has a significantly improved Life Cycle Assessment compared to its predecessor model.”
More information: www.dsm.com