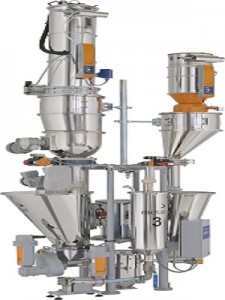
POWTECH, Nuremberg, 23 to 25.04.2013: the raw material processing industry is permanently exposed to increased pressure, demanding satisfaction of highest quality requirements, while simultaneously consistently reducing costs. Conveying, mixing and dosing of materials being processed therefore become extremely important, as precision and consistency here are key factors contributing to product quality and profitability. motan, one of the worldwide leading system suppliers for sustainable material handling, offers a comprehensive programme that covers all areas of dosing and mixing – in particular with continuously regulated gravimetric systems. Trade visitors can find proof of the company’s competence in these areas at the POWTECH in Hall 4 on Stand 347.
METRO P conveys powder profitably
The METRO P powder (P) hopper loaders have been developed for reliable, service-free continuous operation for conveying non-free-flowing and free-flowing raw materials. Formation of lumps and bridging are impossible: this is guaranteed sustainably by the geometries of the discharge openings having been calculated by computer, empirically and under laboratory conditions. The largest equipment, with 1,000 kg/h output, has a 260 mm diameter opening. The METRO P range is constructed in three sizes – with 200 kg/h conveying performance & 10 litres capacity (cycle), with 500 kg/h performance & 25 litres capacity, and 1,000 kg/h performance & 50 litres capacity. The METRO P containers are produced in electro-polished stainless steel which makes them extremely robust and service-friendly.
Conveying of substances and materials in powder form requires use of micro filters in the conveying air environment. motan uses multiple filter cartridges in the METRO P equipment, in the form of Teflon-coated star shaped filters with very large surface area, so that the most minute and finest µm-sized powder dust particle fractions can be “captured”, gathered and filtered out. A battery of four filter cartridges operates in the compact METRO P with its 200 kg/h conveying performance, a battery of seven filter cartridges each in the models with medium (500 kg/h) and high (1,000 kg/h) output performance.
The process is kept clean with automatic air-jet de-dusting while the process is running. Working with a defined sequence schedule, the air-jet return stream is triggered off around one second prior to the end of the conveying cycle, in order to pneumatically unload the appropriate cartridges from within the batteries of four or seven cartridges, by selection of defined cartridges, or sequentially, one after the other.
GRAVIPLUS® – loss-in-weight
All gravimetric mixing and dosing disciplines are ideally covered with the GRAVIPLUS® synchronous dosing and mixing station – in applications such as blown film, cast film, foam extrusion, cable insulation & sheathing extrusion, masterbatch production, compounding, inline compounding, wood plastic composite production, etc. Up to eight dosing modules can be used for granulate, micro-granulate, powder, liquids and regrind. With throughput performance from 0.25 up to 7,500 kg/h and constant dosing precision of ±0.1 % (1:1.000.000 load cell resolution), a level of performance and product certainty is achieved that is essential for continuous production processes. GRAVIPLUS® works according to the loss-in-weight principle.
The material flow is continuously regulated and monitored according to weight, in real time. Bulk density fluctuations and changes in particle size or flow behaviour cannot influence dosing precision. Vibrating wire technology makes the load cells insensitive to both vibration and temperature. Self-calibration means the need to dose out for new materials is eliminated. The components are continuously dosed time-synchronised into the mixing chamber by speed-controlled precision dosing screws. The result of this is that a homogenised mixture reaches the intake zone of the processing machinery. Separation is impossible, even with critical materials. Dosing modules with twin screws and stirrers are used with poorly free-flowing or non-free-flowing materials, weigh-tanks with liquids.
Very easy installation and operation – two important plus points
GRAVIPLUS® is easy and fast to install. The equipment can be emptied and cleaned in several minutes when changing colour or material. Equipment size and height have been significantly reduced, without detriment to line performance, through use of newly developed fast refilling systems (max. 40 refill cycles per hour). Consequently, the conveying system that brings the components to the dosing system also can be made with smaller dimensions. The advantage here: easy installation of the station directly at the processing machinery. It also eliminates the need for an equipment platform (cost reduction). Correspondingly, service tasks such as cleaning, material change and reconstruction are facilitated. Demands for shorter downtimes and simultaneous higher flexibility in operation are therefore completely fulfilled.
GRAVInet GP – the new intelligent control system
The GRAVInet GP control/regulation system is an integral member of the motan CONTROLnet family. This enables it to be perfectly combined with other motan control systems for the areas of storage, conveying, drying, dosing and mixing, etc. For example, this system controls/regulates GRAVIPLUS® with its maximum eight dosing modules, refilling slides and butterfly valves. Integration takes place with an overlaying Web application via Ethernet. The new user-friendly WEBpanel with its 12.1″ TFT touch screen is supplied with GRAVInet GP visualisation software already pre-installed. The user has menu-based access to all functions: operation, process control, recipe management, quality assurance protocols, service, trend charts, etc.
The control system has a completely modular design – logic, HMI (Human Machine Interface), etc. The advantages here: no limitation to the number of dosing modules or lines. For example, more than 12 components or more than four lines can be served. With the GRAVInet GP control system, optimum dosing precision is combined with absolutely reliable production lot repeatability. The real weighed and dosed amounts are compared continually in real time with the set values and displayed in clear language, also as event protocols. Remote service, e.g. software updates, can be carried out via VNC (Virtual Network Computing).
The motan Group
The motan Group, with its headquarters in Konstanz on Lake Constance in Germany, was founded in 1947. As the leading provider of sustainable materials handling, the company is active in injection moulding, blow moulding, extrusion and compounding, in-line systems and chemicals. Part of the application-orientated product spectrum are innovative modular systems solutions for storage, drying, and crystallisation, conveying, dosing and mixing for the plastics manufacturing and processing industries.
Production takes place at various locations in Germany, India and China. motan distributes its products and systems solutions via its regional motan-colortronic centers. Currently, more than 500 employees contribute to an annual turnover of approximately 100 million Euros. As a result of its network and its many years of experience, motan offers its customers what they actually require: solutions with genuine added value.