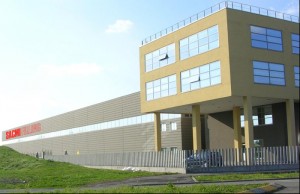
From raw material to bottle, from closure systems to control and inspection systems: Sacmi presents the Chicago-held Pack Expo with a comprehensive range of solutionsSacmi flies to Chicago to present its comprehensive range of technology for the beverage industry at Pack Expo 2012. The Imola-based Group is the only systems and solutions supplier to the industry to have developed its own technology for each of the key systems in the production process. All eyes will, in particular, be on compression technology, which simultaneously ensures very short cycles times, low consumption and contained maintenance costs.
Pack Expo will be held from 28th to 31st October 2012 at McCormick Place South in Chicago, Illinois. With 125 countries taking part, this bi-annual international event is crucial for the packaging industry’s machine and technology sector. Here, industry professionals get together to compare new products and technologies, find out about the latest trends, gather information and, of course, sign commercial agreements.
What Sacmi provides goes far beyond the simple supply of machines and plants. It begins, in fact, with product prototyping services to develop ideas, carry out design work and then proceeds with definition, in close collaboration with the customer, of the best way to go from raw material to PET bottle and on to the final consumer, leaving no aspect of the process uncovered. This is a service that can only come from a true “solutions provider”, capable of developing comprehensive solutions that cover it all from cap and preform to bottle stretch-blowing, labelling and palletization.
Within this comprehensive range of goods and services lie the outstanding advantages of continuous compression moulding. More, specifically, the latest machine to be developed by Sacmi, the CCM48SB, is characterised by excellent production performance (up to 1600 caps per minute), thanks to extremely short cycle times, and very low energy consumption rates of just 0.75 kWh/kg at maximum output rates: that’s a full 25% lower than the best consumption levels recorded with injection technology.
The added value of this technology is boosted even further when a vision system – also Sacmi-made, of course – is added for real-time control of integrated caps and, therefore, minimisation of defects on outgoing products. In this context, the CHS 003 “stand alone” system for the quality control of plastic and aluminium screw caps, which features two suction feed belts and a system using no less than three cameras (with the option of a fourth), ensures complete control of the item: first, the internal surface is checked thanks to the cameras on the first belt, then the exterior is checked with a third, colour camera on the second belt that “explodes” the cap and checks the integrity of its surface, decoration included, point by point. In short: a revolutionary machine able to inspect up to 120,000 pieces an hour!
Huge advantages are offered not only by compression systems. The machines in the SBF (Stretch Blow Forming) range, which have from 6 to 24 stretch-blowing stations, are at the very apex of their category, ensuring output of 64,000 bottles per hour in the standard half-litre format. Advantages on this line include the 1B=2b system, that is, the possibility of installing, on every machine in the range, a one-cavity mould for large bottles (up to 3 litres) or a 2-cavity mould for small bottles (up to 0.6 litres); moreover, the switch from single to double cavity (and vice versa) is extremely simple and fast.
Hourly output may therefore be as high as 2700 small bottles per station, thus making full use of the output capacity and potential of both the machine and any downstream filling line. Moreover, the SACMI Group, via its subsidiary SACMI Filling, also provides a full range of complete liquid food filling machines with cutting-edge technology. Developed entirely in-house in the Parma industrial district thanks to the skill and experience of our designers, these machines are divided into two distinct families: the mechanical range and the electronic range.
The mechanical range consists of two models: Vega isobaric level fillers for sparkling drinks (beer included) and Alfa units for the cold filling of still products (e.g. water) or hot filling with recycle (e.g. juices, isotonic drinks,…). These are simple, hard-wearing, reliable machines of truly outstanding performance. The Electronic range, instead, includes various, more sophisticated models that focus on specialization and flexibility. More specifically: the EWF filler (an electronic volumetric unit for still water with 1 flow meter per valve), the EWS filler (electronic volumetric for still water with a patented system having just one flow meter for the entire machine), the EHA and EHC fillers (electronic volumetric Hot Fill units, without and with valve-bottle contact respectively), the ESF fillers (electronic volumetric for CSD and sparkling water), the ELF (electronic level sensor unit for filling PET bottles with sparkling products), the ELG (for filling glass bottles with sparkling products, beer included), the ELT (long-tube electronic volumetric for filling PET bottles with beer). All machines are accessorized with “ultra clean” filling insulators and efficient CIP systems plus fast size changeover and safety systems that comply with the standards of even the strictest countries.
Moreover, the SACMI Group, with its BEVERAGE division, is a successful provider of turnkey systems that can count on its own System Engineering department specialising in the design of liquid food packaging systems, a Project Management department that coordinates complex projects and a Field Engineering department that installs and starts up complete plants all over the world. Last but not least, the SACMI Group has dozens of branches, organised to follow customers closely and meet their every need on all the main markets. In short: true market leader professionalism and capability plus “tailor-made” customer care.
Importantly there are also the labelling machines, designed in Sacmi Verona with the specific aim of making the labelling process more flexible, higher-performing and cleaner. Leading the way is the series MOD (Modular) technology, an effective response to labelling needs requiring combined technologies. Each module consists of a labelling station fitted on a mobile shuttle that can easily be connected/disconnected from the machine and replaced with another of a different labelling technology [Self-Adhesive (Pressure-Sensitive), Cold Glue, Hot Melt, Roll Fed] and performance. This solution requires far less factory space and also makes it easier to insert the machine into new and/or pre-existing lines.
Moreover, the SACMI labeller series includes the FORMSLEEVE+, which allows high shrink labels to be applied directly from the reel of film. The labels are cut and the sleeve tube is created, applied and shrunk directly onto containers all within the same machine, resulting in considerable savings in efficiency, material, space and energy as well as higher production speeds, than traditional sleeve application systems.